- Safety Information
-
Resources
- Pipeline Member Directory
- Emergency Response Grants and Resources
- Pipeline Member Information
- Request Additional Materials
- Provide Feedback / Request Information
- Mailing List Request Form
- Excavator Resources
- Excavation Safety - 811
- Excavation Safety Checklist - Spanish
- Public Officials Resources
- Government & Industry Links
- Emergency Responder Engagement
- Emergency Response Training Resources
- Emergency Response Capabilities
- PipeVision Mapping Application
- Pipeline Safety Video Library
-
Sustaining Members
- Hawaii Pipeline Safety Association
- Montana Liquid & Gas Pipeline Association
- North Dakota Pipeline Association
- Pipeline Association of the Northwest
- Pipeline Operators of Colorado
- South Dakota Pipeline Association
- Utah Pipeline Association
- Wyoming Pipeline Association
- All Sustaining Member Organizations
- Member Resources
Glossary of Terms
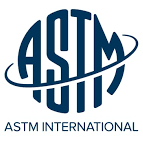
From the web site of the ASTM International: Founded in 1898, ASTM International is a not-for-profit organization that provides a global forum for the development and publication of voluntary consensus standards for materials, products, systems, and services. Formerly known as the American Society for Testing and Materials, ASTM International provides standards that are accepted and used in research and development, product testing, quality systems, and commercial transactions around the globe. ASTM International can be reached at 610-832-9585 or for more information see www.astm.org.
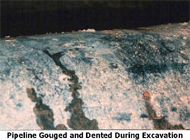
An accident is an unplanned occurrence that results in a release of oil or natural gas from the pipeline. Accidents can be expensive and can sometimes result in extensive property loss, environmental insult, injury and, sometimes, even death. Accidents can result from a lot of reasons, but the biggest reason is from damage to the pipeline resulting from digging. Technically speaking: As used in pipeline safety regulations, accidents are failures operator must make a report to the Office of Pipeline Safety. Specific criteria defining events that are considered accidents are contained in 49CFR 195.50. Events or failures of similar magnitude related to gas pipelines are considered incidents and are defined in 49CFR 191.3. occurring in liquid pipeline systems for which the pipeline
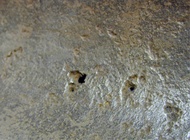
Active corrosion is a term that indicates that pipeline corrosion is occurring now and is deteriorating the pipe. Technically speaking: Active corrosion describes an ongoing electro-chemical process in which microscopic metal particles are removed from iron-based materials. Corrosion can occur in moist, aboveground atmospheric conditions but is more prevalent in underground environments. Active corrosion within the pipeline industry is a serious threat to pressure containing structures (i.e., steel pipelines) that, unless controlled, could result in leaks or failures. See Also: Corrosion
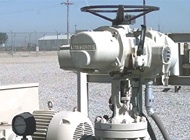
An actuator is a device that causes a valve to move from the open to the closed position or vice versa. Technically speaking: A component designed to provide the mechanical energy to physically move a connected device. Actuators are used extensively to move valves to their open and closed positions. Valve actuators can be pneumatic, hydraulic, or electric motor driven and can be automated to respond to a remote control signal.
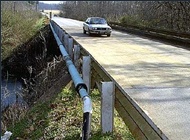
An aerial river crossing is a location where a pipeline is suspended to cross a waterway, either by cables over the waterway or attached to the girders of a bridge designed to normally carry vehicle traffic.

From the web site of the American Gas Association: The American Gas Association represents 200 local energy utility companies that deliver natural gas to more than 64 million homes, businesses and industries throughout the United States. AGA’s members deliver 92 percent of all natural gas provided by the nation’s natural gas utilities. AGA is an advocate for natural gas utility companies and their customers and provides a broad range of programs and services for member natural gas pipelines, marketers, gatherers, international natural gas companies and industry associates. AGA can be contacted at 202-824-7000 or for more information see www.aga.org.
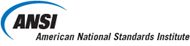
From the web site of the American National Standards Institute: The American National Standards Institute (ANSI) is a private, non-profit organization (501(c)3) that administers and coordinates the U.S. voluntary standardization and conformity assessment system. The Institute’s mission is to enhance both the global competitiveness of U.S. business and the U.S. quality of life by promoting and facilitating voluntary consensus standards and conformity assessment systems, and safeguarding their integrity. ANSI can be contacted at 212-642-4900 or for more information see www.ansi.org.
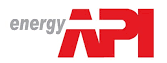
From the web site of the American Petroleum Institute: The American Petroleum Institute (API) is the major national trade association representing the entire petroleum industry: exploration and production, transportation, refining, and marketing. With headquarters in Washington, D.C., and petroleum councils in 33 states, it is a forum for all parts of the oil and natural gas industry to pursue priority public policy objectives and advance the interests of the industry in a legally appropriate manner. API can be contacted at 202-682-8000 or for more information see www.api.org.
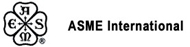
From the web site of the American Society of Mechanical Engineers: The American Society of Mechanical Engineers (ASME) conducts one of the world’s largest technical publishing operations, holds some 30 technical conferences and 200 professional development courses each year, and sets many industrial and manufacturing standards. Founded in 1880 as the American Society of Mechanical Engineers, today ASME International is a nonprofit educational and technical organization serving a worldwide membership. ASME can be contacted at 1-800-843-2763 or for more information see www.asme.org.
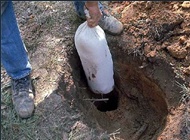
An anode is the pole or terminal from which current flows in a direct current electrical circuit. In an electrical cell or battery(such as a flashlight battery), the anode is recognized as the negative terminal. When a completed circuit exists (as when you turn on the flashlight), electrical current flows from the negative terminal (the anode) through the circuit to the positive terminal (the cathode). Along the way, the current lights the flashlight bulb. As the anode gives up electrons it deteriorates, or corrodes. Technically speaking: An anode is the electrode in an electrochemical corrosion cell where oxidation or corrosion occurs and from which current flows. In a pipeline-related cathodic protection system, the anode is the sacrificial material or electrode having low electrolytic potential. Current flows away from the anode, causing it to corrode. Corrosion of the anode protects a nearby structure (pipeline, tank bottom, or other underground structure) having higher electrolytic potential from corroding.
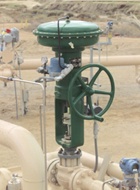
An automatic control valve is a valve that controls the flow of oil or natural gas in a pipeline and that opens or closes automatically in response to some signal. Technically speaking: An automatic control valve is one that closes automatically in response to a pressure loss or a flow rate increase, either of which exceeds a predetermined set point.
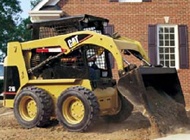
Backfilling means filling the dirt back into a ditch or hole you previously dug. Technically speaking: Backfilling is the process of filling the trench where a newly constructed or recently unearthed pipeline is installed. Adequate fill material is provided and compacted around the pipe to completely fill the excavation and to ensure that the pipe is properly supported and not subjected to added stresses due to soil subsidence or movement.
(1) A barrel is a standard measure of a volume of oil and is equal to 42 gallons. (2) A beginning point or end point of a pipeline is sometimes referred to as a barrel. Barrels are designed with opening closures similar to doors that allow the pipeline operator to insert inline inspection tools into the pipelines. Barrels where pigs are inserted into the pipeline are called launchers and barrels where pigs are retrieved and taken out of the pipeline are called receivers. Reference 49CFR 194.5 and 49CFR 195.2
A baseline assessment plan (BAP) is the plan a pipeline operator must develop to assess the integrity of all of the lines included in its integrity management program. The BAP must show when each line is to be assessed and the assessment method the operator will use. Technically speaking: The baseline assessment plan is an integral part of an operator’s pipeline integrity management program. The BAP must, as a minimum: 1) identify all segments of a pipeline system that could impact a High Consequence Area (HCA); 2) identify the specific integrity assessment method(s) to be conducted on those segments; 3) specify the schedule by which those integrity assessments will be performed; and 4) provide the technical justification for the selection of the integrity assessment method(s) and the risk basis for establishing the assessment schedule. (Reference 49CFR 195.452).
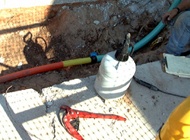
A bell hole is a hole dug into the ground over or alongside a pipeline to allow the line to be examined and to provide room for workmen to perform maintenance on the pipeline. In a broader sense it is any hole, other than a ditch, that is opened for pipeline work. Technically speaking: A bell hole is an excavation made to permit a survey, inspection, maintenance, repair, or replacement of pipe sections. It is so called because of its upside-down bell shape, wide at the top and narrowing to a smaller diameter around the pipeline to be examined. The walls of the hole are angled according to OSHA rules to prevent cave-ins and risks to worker safety.
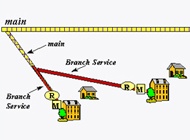
A branch service line is a service line in a natural gas distribution system that branches off of a main line or another service line. Technically speaking: In natural gas distribution systems, branch service line is a line that branches off of another service line; thereby changing the classification upstream of the branch point from a service line to a main.
A breakout tank is a tank used to temporarily store oil in a pipeline system. Technically speaking: A breakout tank is a tank used to relieve surges in a hazardous liquid pipeline system or to receive and store hazardous liquids transported by the pipeline for later re-injection and continued transportation by the pipeline. Reference 49CFR 194.5 and 49CFR 195.2.
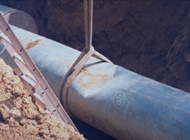
A buckle is an anomaly that represents a partial collapse of the pipe wall and is usually caused by excessive bending or curvature being applied to the pipe. Depending on the severity of the buckle, it may represent an undesirable anomaly that can cause localized stress concentrations and must be repaired. Technically speaking: A buckle is a partial collapse of the pipe wall due to excessive bending associated with soil instability, landslides, washouts, frost heaves, earthquakes, etc. Buckles can also occur in pipeline construction during a field bending operation using a side boom. Buckles cause localized stressconcentrations and must not be installed in new construction or, if found, must be removed from existing systems. See also: Wrinkle
From the web site of the Bureau of Land Management: The Bureau of Land Management (BLM) is an agency in the Department of Interior, in the US Government. The BLM manages 264 million acres of surface acres of public lands located primarily in the 12 Western States, including Alaska. The agency manages an additional 300 million acres of below ground mineral estate located throughout the country. The BLM administers public lands within a framework of numerous laws. The most comprehensive of these is the Federal Land Policy and Management Act of 1976 (FLPMA). All Bureau policies, procedures and management actions must be consistent with FLPMA and the other laws that govern use of the public lands. It is the mission of the Bureau of Land Management to sustain the health, diversity and productivity of the public lands for the use and enjoyment of present and future generations. The BLM can be contacted at 202-452-5125 or for more information see www.blm.gov.
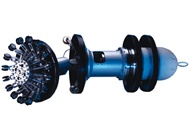
A caliper tool is an adjustable measuring tool that can be used to measure the thickness of an object, the diameter of a circle, or the distance between two surfaces. Hi-tech variations of these tools are used to measure the inside diameter of a pipe and record variations in that diameter. Technically speaking: A caliper tool is an inline inspection device that measures deviations in the geometry of a pipeline’s internal surface. A caliper tool uses a set of mechanical fingers that ride against the inside diameter of the pipe and record deviations caused by the relative movement of these fingers as the tool passes through the pipe
Carbon dioxide is a naturally occurring gas that is transported and used in the petroleum industry. Carbon dioxide is a heavy gas that can displace breathing air and breathing carbon dioxide can be hazardous to your health. Technically speaking: Carbon dioxide is a naturally occurring gas consisting of molecules formed of one carbon and two oxygen atoms. Carbon dioxide is a heavy gas that is transported by pipeline as a compressed fluid consisting of more than 90% carbon dioxide molecules. If released into the atmosphere from a pipeline leak carbon dioxide is considered hazardous due to its ability to displace breathing air. (Reference 49CFR 195.2)
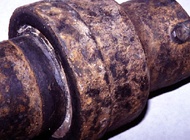
Cast iron is iron that is cast (heated to melting and poured into molds) and in which the carbon molecules in the metal are not bonded with the iron molecules. Cast iron is brittle and can crack. It is not suitable for high-pressure applications. Technically speaking: Cast iron applies to gray cast iron, which is a cast ferrous material in which a major part of the carbon content occurs as free carbon in the form of flakes interspersed through the metal. Because the carbon flakes do not bond with the ferrous material on the molecular level, the metal is brittle and susceptible to stress cracking under high-pressure situations. Many older, low-pressure gas systems were constructed with cast iron pipe.
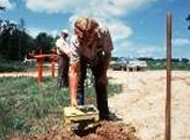
Cathodic protection is a method of protecting metallic pipelines from corrosion. Technically speaking: Cathodic protection is a method of corrosion prevention in which the pipeline is allowed or made to act as the cathode in an electrochemical corrosion cell. A sacrificial anode having a lower electrolytic potential than the pipe is provided to complete the cell. The same electrolytic action that causes the anode to corrode protects the cathode (the pipeline or other component) from corroding.
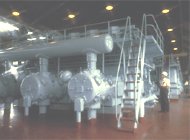
Centrifugal compressors are pumps that are used to boost the internal pressure of gas pipelines. They are usually placed at key locations along the pipeline systems.
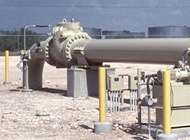
A check valve is a valve that allows liquids or gases in a pipeline to flow in one direction but closes to prevent flow in the opposite direction. These types of valves are used extensively in the pipeline industry to prevent reverse-flow or back-flow in the event of a pipeline leak or abnormal operating occurrence.
Class location refers to a regulatory designation for natural gas transmission pipelines that indicates the level of human population within a certain distance on either side of the line. The class location of a pipeline is a factor in determining the maximum allowable operating pressure of the pipeline. Technically speaking: Class location is a criterion for gas pipeline design set by the U.S. Code of Federal Regulations, 49CFR 192.5. A class location is based on the number and type of buildings intended for human occupancy that are situated in an area that extends 220 yd (200 m) on either side of the centerline of any continuous 1.0-mile (1.6-km) length of a gas pipeline. Class locations are specified as Class 1, 2, 3 or 4. Class 1 indicates the least heavily populated of the class locations, representing an offshore area or an area with 10 or fewer buildings intended for human occupancy. In comparison, Class 4 indicates the most heavily populated of the class locations, representing an area where buildings with four or more stories above ground are prevalent.
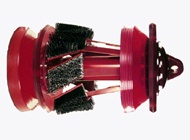
A cleaning pig is a device that is placed inside a pipeline to remove unwanted debris from the inside of the pipeline. The pig can be drawn or pushed through a pipeline but often is moved through the line as a result of the flow of the product in the line. A type of utility pig, a cleaning pig uses cups, scrapers, or brushes to remove dirt, rust, mill scale, and other debris from the internal surface of a pipeline. Cleaning pigs are used periodically or as necessary to increase the operating efficiency of a pipeline or to facilitate inspection of the pipeline.
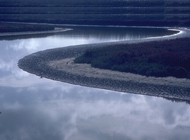
A commercially navigable waterway is a waterway where there is a substantial likelihood of commercial navigation. These waterways are identified in the National Waterways Network, a geographic database created by the National Waterways GIS Design Committee. The database is available from the U. S. Department of Transportation, Bureau of Transportation Statistics.
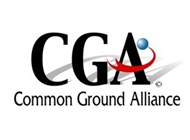
From the web site of the Common Ground Alliance: The Common Ground Alliance (CGA) is a nonprofit organization dedicated to shared responsibility in damage prevention and promotion of the damage prevention Best Practices identified in the Common Ground Study Report. The purpose of the CGA is to ensure public safety, environmental protection, and the integrity of services by promoting effective damage prevention practices. The CGA can be reached at 703-818-3217 or for more information see www.commongroundalliance.com.
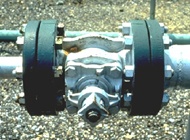
A component in a pipeline system is any part of the system that is subject to the internal system pressure. System components must be designed to not leak; thereby assuring that the oil or gas is not released from the system and that the system operating pressure is maintained. Examples of components include the pipe, valves, flanges and other fittings.
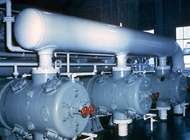
Compressor Stations are facilities located along a natural gas pipeline which house and protect compressors. Compressors are used to compress (or pump) the gas to move it through the system. Compressor stations are strategically placed along the pipeline to boost the system pressure to maintain required flow rates.
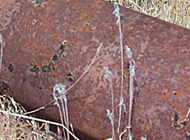
Corrosion is the deterioration of a material, usually a metal, which results from a reaction with its environment. Common rust is an example of corrosion of iron. Steel pipe is subject to corrosion damage. See Also: Active Corrosion, Atmospheric Corrosion, Corrosion Fatigue, Non-active Corrosion, Pitting, Selective Corrosion, Stress Corrosion Cracking (SCC), Uniform Corrosion
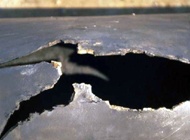
Cracks are undesired openings or separations in a normally rigid material, such as a pipe wall. Often cracks are found only on the surface and do not fully penetrate the pipe wall. Using specialized equipment, cracks that may not appear on the surface of the pipe can be found within the thickness of the pipe wall. Regardless, cracks that don’t fully penetrate the pipe wall and result in leaks are considered critical anomalies that could propagate into a leak or failure and must be repaired. Technically speaking: Cracks in line pipe are separations in the molecular structure of the base metal and form as a result of improper manufacturing or operational stresses. Cracks are detrimental to the pipe’s pressure restraining capabilities and can propagate into complete failure or rupture zones.
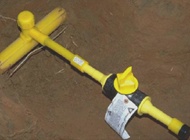
A curb valve is a valve installed in a natural gas service line and is used to shut off the gas supply to a building. Curb valves are installed underground at or near the property line, normally with protective curb boxes or standpipes installed over or around the valve. They are operated by use of a removable key or specialized wrench.
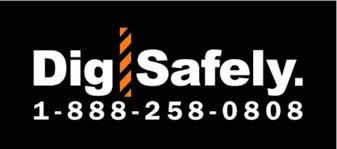
In addition to enforcing Damage Prevention Regulations in the Code of Federal Regulations, the Office of Pipeline Safety has undertaken a variety of other initiatives to promote pipeline damage prevention. These initiatives, some of which involve collaboration with various stakeholder industry groups, promote public awareness of pipelines and other underground facilities; education of the public and emergency officials, excavators, emergency responders, legislators and other stakeholders on how to recognize and respond to pipeline leaks; and other aspects of pipeline safety. Some more notable recent efforts include: Dig Safely, Common Ground Alliance (CGA), and the One-Call Systems Study (OCSS).
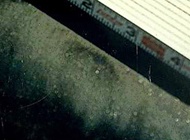
A defect is an imperfection that can cause an inadequacy or failure. In pipelines, certain types of defects have been known to cause failures. When defects are found in a pipeline that are characteristic of problem defects, they must be evaluated and, if necessary, repaired or removed to prevent future failures. Technically speaking: A defect is an imperfection of sufficient magnitude in a pipeline that it should be analyzed using a recognized and approved engineering procedure, such as ASME B31G. Analysis determines if the defect is severe enough to require removal or repair, depending on prescribed operating requirements. Examples of defects include dents, corrosion pits, and cracks.
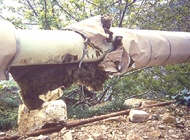
A dent is a depression in the pipeline surface caused by pressure or a blow. A dent does not reduce the thickness of the pipe wall. Dents are usually local depressions caused by outside mechanical force, such as the pipe resting on a rock or being hit by a backhoe. Pipeline repairs or replacement may be needed depending on the severity of the deformation.
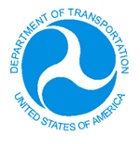
From the DOT web site: A cabinet-level department of the executive branch of the federal government. The DOT is headed by the Secretary of Transportation, who is appointed by the President and confirmed by the Senate. The DOT is responsible for government involvement in all types of transportation, including transportation of hazardous liquids and natural gas by pipeline. Within the DOT, the Office of Pipeline Safety, part of the Research and Development Administration, is responsible for regulating pipeline safety. The Department of Transportation can be contacted at 202-366-4000 or for more information see www.dot.gov.
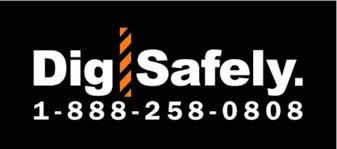
Dig Safely is the nationally recognized campaign to enhance safety, environmental protection, and service reliability by reducing underground facility damage. This damage prevention education and awareness program is used by pipeline companies, one-call centers, and others throughout the country. Dig Safely was developed through the joint efforts of the Office of Pipeline Safety and various damage prevention stakeholder organizations. Dig Safely is now within the purview of the Common Ground Alliance (CGA). The CGA can be reached at 703-818-3217 or for more information see www.commongroundalliance.com.
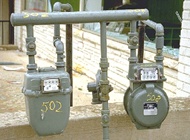
A distribution line is a line used to supply natural gas to the consumer. A distribution line is located in a network of piping located downstream of a natural gas transmission line. As defined in natural gas pipeline safety regulations, a distribution line is a pipeline other than a gathering or transmission line.
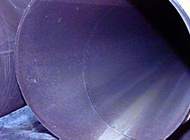
Double-submerged arc-welded pipe is pipe produced from a flat piece of steel of which the edges are rolled together, to create a tube or pipe, and then connected or ‘fused’ together utilizing a specific process known as double-submerged arc-welding. Technically speaking: Double-submerged arc-welded pipe is pipe having a longitudinal or spiral seam produced by at least two weld passes, including at least one pass each on the inside and outside of the pipe. The molten weld metal is shielded by a blanket of granular, fusible material used to reduce the impurities (slag) introduced from the surrounding air. Mechanical pressure is not used and filler metal for the inside and outside welds is obtained from the electrode(s). Use of DSAW in pipe fabrication is required by some pipe design standards, e.g., ASTM A-381, API 5L.
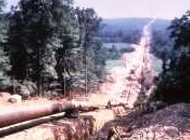
An easement is an acquired privilege or right, such as a right-of-way, afforded a person or company to make limited use of another person’s or company’s real property. For example, the municipal water company may have an easement across your property for the purpose of installing and maintaining a water line. Similarly, oil and natural gas pipeline companies acquire easements from property owners to establish rights-of-way for construction and operation of their pipelines.
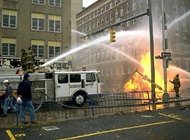
Emergency response personnel are persons engaged in the immediate response to accidents and emergencies. Emergency response personnel can include firefighters, police/sheriffs, medical personnel, civil defense and emergency management personnel, and, sometimes, military, manufacturing and transportation personnel. Emergency response personnel are sometimes referred to as ’emergency responders’ and ‘first responders.’
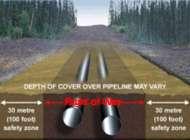
Encroachment refers to the unauthorized use of a right-of-way in violation of the terms by which the right-of-way was established (e.g., easement).
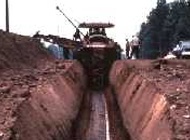
Excavation refers to any operation involving movement of earth, rock or other materials below existing grade or surface level. Excavation can include digging, blasting, boring, tunneling, and backfilling.
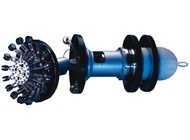
Geometry tools are inline inspection tools that are used to identify changes in the internal shape/diameter of a pipeline. Changes in the internal shape or diameter of pipe can be caused by dents, wrinkles, ovality, bend radius and angle, and occasionally indications of significant internal corrosion.
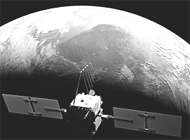
Global Positioning System is a satellite navigation system funded and controlled by the U. S. Department of Defense (DOD). While there are many thousands of civil users of GPS world-wide, the system was designed for and is operated by the U. S. military. GPS provides specially coded satellite signals that can be processed in a GPS receiver, enabling the receiver to compute precise position, velocity and time. The space segment of GPS consists of the GPS satellites that send radio signals from space. The nominal GPS Operational Constellation consists of 24 satellites that orbit the earth in 12 hours. There are often more than 24 operational satellites as new ones are launched to replace older satellites. Four GPS satellite signals are used to compute the position of a receiver in three dimensions and the time offset (velocity) in the receiver clock.
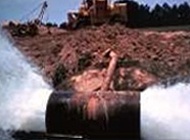
Hydrostatic pressure testing (or ‘hydro testing’) is a method of testing pipeline integrity in which the line is filled with a liquid, usually water, and then the pressure of the liquid is raised to a specified pressure that is maintained for a specified period of time. Any ruptures or leaks revealed during the test must be repaired and the test repeated until no problems are noted.
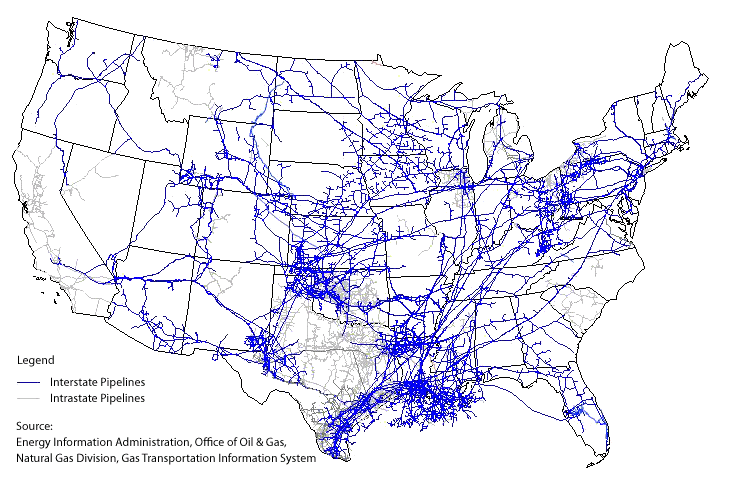
An interstate pipeline is a pipeline that extends beyond the boundaries of one state. Technically speaking: An interstate pipeline is a pipeline or that part of a pipeline that is used in transportation of hazardous liquids or natural gas in interstate or foreign commerce.
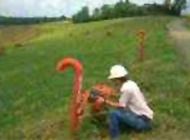
A leak survey is a systematic inspection for the purpose of finding leaks on a pipeline. The frequency and methods of performing leak surveys are regulated and may vary depending on several factors.
Communication for establishing and maintaining mutual understanding and cooperation.
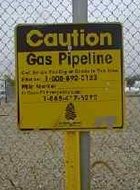
Line markers are signs or other markers installed above the pipeline to indicate the approximate pipeline route and provide emergency phone numbers. Requirements for line markers are specified in federal pipeline safety regulations. (Reference 49CFR 192.707 or 49CFR 195.410)
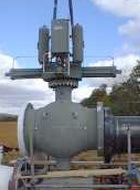
A mainline valve is a valve positioned at a location along the pipeline system that can be closed down to isolate a line section in an emergency. Mainline valves are especially important to minimize hazards and damage or pollution from an accidental release of oil or natural gas. Mainline valves may also be referred to as sectionalizing block valves for natural gas pipelines. (Reference 49CFR 192.179 and 49CFR 195.260)
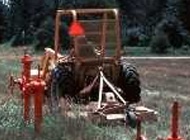
Maintenance is the process of maintaining property or equipment, including pipelines, to preserve it and prevent it from failure and ensure that it will continue to perform its intended function.
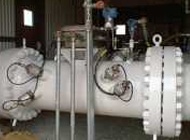
Metering and regulating stations are installations containing equipment to measure the amount of gasentering or leaving a pipeline system and, sometimes, to regulate gas pressure.
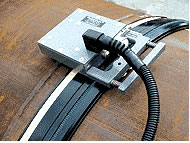
Nondestructive testing is material testing in which the part being tested is not destroyed or rendered unusable. Technically speaking: Pipeline NDT typically consists of: 1. Radiography (X-rays): identifies laminations and weld discontinuities. 2. Ultrasonics: locates lamination in the walls of pipe; determines wall thicknesses. 3. Magnetic particle inspection: tests for surface cracks in welds and component bodies. 4. Dye penetrant: locates surface cracks in welds or component bodies. 5. Ammonium persulfate: identifies hard spots in welds due to arc burns. See Also: Destructive Testing A CMOS scanner being used on a pipeline girth weld. Photo courtesy of American Welding Society
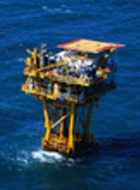
An offshore pipeline is a pipeline located off the coast of the United States. Large quantities of natural gas and crude oil are produced from beneath the ocean floor. Offshore pipelines transport these products from the offshore production areas to onshore processing plants and pipelines. Technically speaking: An offshore pipeline is a pipeline located beyond the line of ordinary low water along that portion of the coast of the United States that is in direct contact with the open seas or beyond the line marking the seaward limit of inland waters.
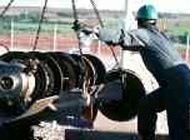
Pig is a generic term signifying any independent, self-contained device, tool, or vehicle that is inserted into and moves through the interior of a pipeline for inspecting, dimensioning, or cleaning. These tools are commonly referred to as ‘pigs’ because of the occasional squealing noises that can be heard as they travel through the pipe. See Also: Inline Inspection Tool
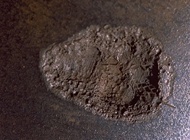
Pitting is Metal loss causing the formation of small depressions in a metallic surface. Pitting may be the result of sand blasting, mechanical gouging, acid etching or corrosion. See Also: Corrosion
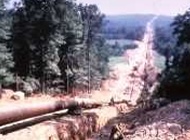
A rights-of-way is a defined strip of land on which an operator has the rights to construct, operate, and/or maintain a pipeline. A ROW may be owned outright by the operator or an easement may be acquired for specific use of the ROW.
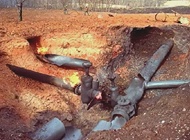
A rupture is the process or instance of breaking open or bursting, as in the rupture of a pipe. Technically speaking: A rupture is the propagation or growth of a defect to such an extent that the pipe becomes completely unserviceable.
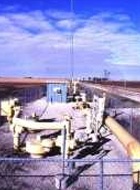
A SCADA is a pipeline control system designed to gather information such as pipeline pressures and flow rates from remote locations and regularly transmit this information to a central control facility where the data can be monitored and analyzed. Through this same system, the central control facility can often issue commands to the remote sites for actions such as opening and closing valves and starting and stopping pumps.
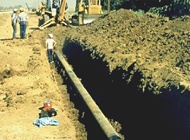
A trench is a long narrow ditch dug into the ground and embanked with its own soil and used for concealment and protection of line pipe. Trenches are usually dug by a backhoe or by a specialized digging machine. See Also: Backfilling